Raymond Lean Management
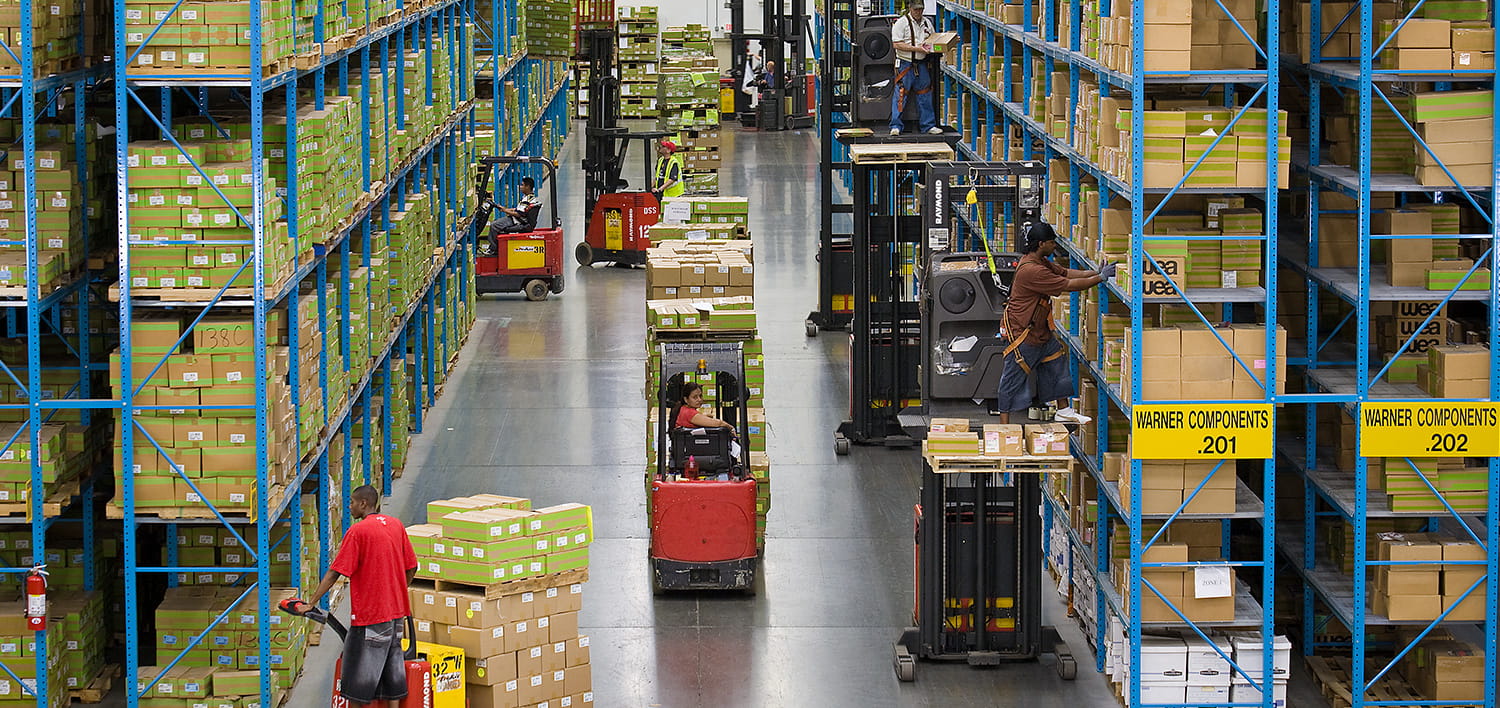
Raymond Lean Management
-
Raymond Lean Management
Over ten years ago, Raymond embarked on a journey to implement the Toyota Production System on its manufacturing floor. This has led to a culture of Continuous Improvement that has solidified Raymond’s reputation for quality and innovation in the marketplace.
Through Raymond’s success in implementing TPS they set out and began a dealer initiative to help dealers learn and implement the same principles and philosophies of Toyota Production Systems (TPS/5S). Presently 20+ Dealers in North America are participating in TPS. -
Johnston Equipment has begun the TPS journey of implementing Raymond Lean Management. Our aim is to optimize and manage the flow of materials through our shops, distribution and warehousing networks.
The Toyota Production System encourages the participation of all employees, so improvements are made across the organization. We know that a journey of Continuous Improvement never ends. There are always improvements that can be made to improve our processes and the customer experience. -
Lean methodology has its roots in manufacturing and particularly the automotive sector through the Toyota Production System. Over the last decade, Lean has expanded beyond manufacturing to become a methodology for all value streams looking to improve efficiency and customer value.
A foundational level of understanding of Lean principles can have a significant effect on a business by:
- Removing non-value added business steps that does not transform the product and/or service
- Identifying and eliminating waste
- Kaizen (“Kai” = Change + “Zen” = For the better) small incremental improvements lead by employee’s
- Improving external partnerships
- Heightening communication and collaboration
- Increasing employee morale and job satisfaction
- Removing non-value added business steps that does not transform the product and/or service